In order to avoid leaving marks on the mold parting surfaces that are supplied by mold manufacturers, it is strictly forbidden to use manual polishing. Currently, a sizeable number of domestic manufacturers are unable to fulfill this requirement because it is not something that they are capable of doing lost wax casting. Generally speaking, it is anticipated that general intermediate molds, which are of a size that falls somewhere in the middle of small and medium, will be able to satisfy this requirement.
When conducting a test of the precision mold design level, it is necessary to ascertain whether or not the rationality of the design and the simplification of optimization are at their highest possible levels. In some circles, this test is also referred to as the test of perfection in mold design. Manufacturers of molds in China continue to display a significant amount of variation in their business practices. The process of determining whether or not you have regular CNC equipment and whether or not you are processing it using the appropriate procedure is what we mean when we talk about testing the equipment level.
This is the process that we are referring to when we say that we are testing the equipment."The mold manufacturing equipment that is currently considered to be the most cutting-edge of any manufacturer anywhere in the world is located in China. This is the case at the present time. A growing number of businesses are coming to the realization
lost wax casting that they are of great significance, and this trend is expected to continue increasing. Finding a solution to the problem of deformation that is caused by internal stress that is incurred throughout the entire process is necessary in order to minimize the amount of deformation that occurs during the processing of mold parts.
This is because the problem of deformation is caused by the presence of internal stress. At this point in the process, we are in the second step. During the process of being cut into mold parts, the material that is being processed continues to suffer from the accumulation of internal stress. The stress that is being experienced continues to build up throughout the process. In an effort to alleviate the stress that is experienced on the inside of the body, the cumulative effect makes an effort to reduce overall stress. method or strategy to take. At this point, the level of internal stress that has been accumulated reaches a certain threshold, which ultimately leads to this happening.
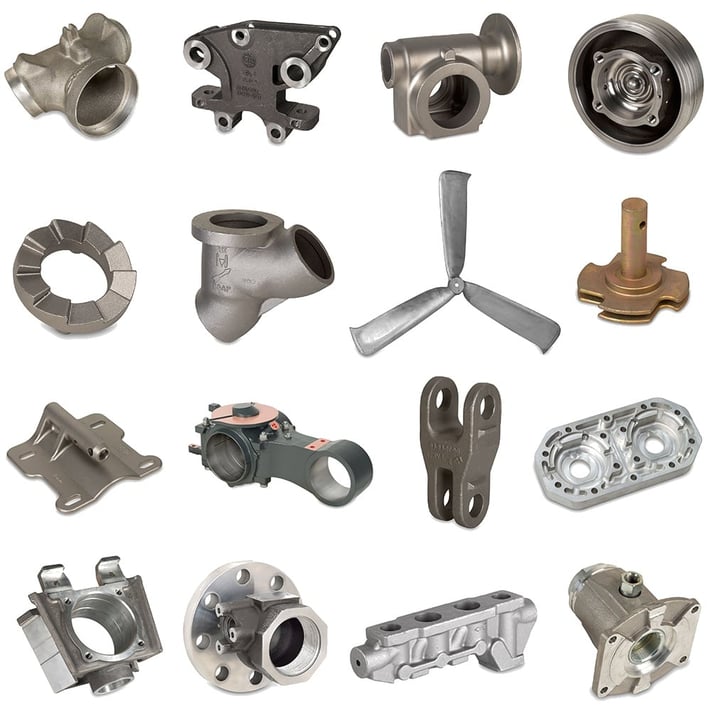
The material that is being processed will invariably accumulate internal stress as the cutting process progresses, which will invariably result in the mold parts becoming deformed. This will occur regardless of whether the material is being cut or not. It makes no difference whether the material is being cut or not; this will take place either way. Regarding this specific matter, we are all in possession of information that is considered to be common knowledge. Overcoming this tendency is necessary in order to defeat the deformation that is brought about by the internal force of precision mold parts. This deformation is brought about by those parts. The elimination of internal stress and mechanical reprocessing, or the combination of the two, are the two methods that can be utilized. Both of these methods present the possibility of being utilized.
The application of heat therapy, which is most commonly referred to as stress relief, is typically utilized for the purpose of alleviating the effects of stress that is experienced on the inside. This is the most common reason for its utilization. On average, the amount of time necessary to complete this process is somewhere in the range of twenty-four to forty-eight hours. In general, aluminum components are placed inside the furnace, where they are heated to a temperature of 290 degrees Celsius over the course of six hours, maintained at a warm temperature for two to four hours (depending on the size and thickness of the workpiece, as well as the temperature of the local season), and then cooled inside the furnace. This process is repeated until the components reach the desired temperature. Once the components have reached the desired temperature, this process
Ductile Cast Iron is repeated until it is complete. The vast majority of situations typically involve the utilization of multiple diagonal methods for the purpose of securing, loosening, and tightening various things. During the process of machining, the datum plane experiences deformation as a consequence of the accumulation of internal stress that takes place. This cause the datum plane to go through the process of suffering deformation.
There was a correlation between the machining process and the observed deformation occurrence. The trimming process is responsible for bringing about a significant amount of change that occurs during the assembly process aluminum die casting. This change, when taken into consideration as a whole, has an effect that is cumulative on the quality of the mold as well as its lifespan.
In order to ensure that the performance of precision molds is in accordance with the requirements of the design, it is necessary to find a solution to the common problem of overcoming deformation that is brought on by internal stress during the manufacturing process of molds. Find a solution to this problem. Deformation occurs as a consequence of the molds being subjected to stress from within, which is the reason for this phenomenon. In rough machining, it is common practice to select a number of surfaces operating in a variety of directions to serve as observation surfaces.
https://fractory.com/wp-content/uploads/2020/02/CNC-milling-1.jpg.webp
This enables the operator to observe the surface being machined. By utilizing this method, we are able to independently determine the extent of the three-dimensional deformation that occurs during the working process. This deformation takes place whenever the material is being worked on. Because of this, the additional observation surface must not be too small; therefore, the observation will be inaccurate if it is too small. Consequently, the observation must not be too small. The purpose of this endeavor Ductile Cast Iron is to enhance its size while simultaneously simplifying the process of removing it to the greatest extent possible. As an illustration, when it comes to a component that has a three-dimensional dimension of 1000×800×300mm, it is generally recommended to establish the length of the observation surface to be at least 900mm, 600mm, or 260mm.
This is because these measurements are considered to be the most accurate measurements. Specifically, this is due to the fact that these measurements constitute the most prominent recommendations.
If the length of the observation surface is only fifty percent of the length of the actual workpiece, then the value that is measured will, in general, be one to two times different from the actual length. This is because the length of the observation surface is only fifty percent in length. The length of the observation surface is relatively short, which is the reason for this. After you have finished doing that, you should then
aluminum die casting proceed to measure the actual data of each observation surface of the workpiece, and after that, you should compare the two phases. In general, you will be able to determine the degree of deformation that the workpiece that is being processed has undergone once it has been processed. Which one of these is the most difficult to accomplish? Immediately following the process of turning the workpiece over, it is essential to pad the workpiece in a flat position before beginning to trim the original datum surface.
This is done in order to guarantee that the workpiece is in accordance with the deformation data that was measured following the rough machining process. In the event that the processing are carried out without padding, the shape of other components will be offset, which will result in excessive cutting in certain components, no cutting at all in certain components, or even negative concavity. This will occur because the shape of the other components will be offset. This effect will take place as a result of the shape of the other components being subtracted from one another. The processing that is being done is being done with the purpose of preventing the datum plane from becoming deformed. This will allow the datum plane to continue to function as the first datum plane.